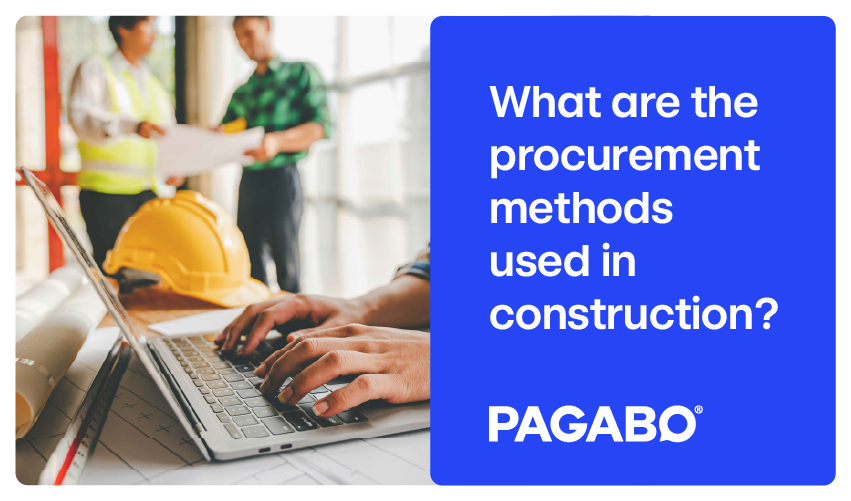
In construction, procurement is the process of acquiring goods and services as it is in other industries. For successful project delivery, a project manager needs to have a solid procurement process in place to ensure maximum efficiency. How this process is handled has a major impact on the operation and needs to build in the most cost-effective supply purchases, while considering timelines, quality, and budget – which for the kind of large-scale projects undertaken within the construction sector is of utmost importance.
The chosen procurement option is a critical deciding factor on the overall profitability and is vitally important to the success of any construction project.
To ensure a suitable procurement process that matches the needs of the project, stakeholders must identify the risks. Procurement methods are not a one size fits all approach and their relevance will depend on the type of project.
There are four common procurement systems being exercised in industry and it is recommended to fully understand each of them in order to ensure the right method is selected for the job.
Traditional method
Probably the most basic method of procurement, but one that has been well utilised within the construction industry. The responsibility of a contractor is limited only to build, leaving all design works and contract management to a consultant or engineer. The finance and operation are also controlled by the client.
The main advantage of the traditional method is its established parameters that have been laid out for assessing the value for money of this type of procurement path. However, the contractor has less influence as an operational party in the design cost and risk allocation, so there are some disadvantages, which demonstrate why having all parties involved in a scheme from as early as possible is important.
It’s a recommended method for complex and larger projects.
Management contracting
Different from the traditional method, management contracting is the main choice for complex projects. In addition to the client, the consultants, contractors and specialised contractors become a participant. The contractor acts as a manager for the project, overseeing subcontractors, whereas specialised contractors undertake the real build aspect in their chosen field.
The client will only communicate with the management contractors and the client’s risk will be transferred to them.
This method will be chosen if there are possibilities to identify projects in packages.
Design and build
As the name suggests, this method means the design and build elements are left completely to the contractor instead of responsibilities being split out. This means closer collaboration is required in the process and all risks are allocated to the contractor.
Once the design has been created, the client will complete a review and ask the contractor to make any necessary adjustments. Finally, an agreed construction and execution cost will be agreed for the project. The main advantage of a design and build procurement route is the client should not need to appoint a specific design consultant for the project.
Joint venturing/partnering
A joint venture allows two or more separate entities to be responsible for a project. This enables the parties to share both rewards – and risks. In order to establish a joint venture, a new business is created to which each party contributes resources – this could be land, capital, intellectual property, skills, credentials or equipment.
Many of the problems that exist in construction are attributed to barriers that are found between parties of contract. Joint ventures are a solution to overcoming these barriers, by creating a working environment based on mutual objectives, teamwork, and trust.
Identifying the responsibilities of each party can be difficult in a joint venture procurement system, but they are an increasingly common choice to enable smaller companies to deliver larger projects by combining expertise. The smaller companies can then benefit from the credibility and financial stability of the larger company.
Equally, a larger company may opt for a joint venture to acquire new or specialist resources from a smaller company. Overall, it is a good option to gain knowledge in overseas markets and share risks and costs.
In order to work effectively, it’s important there is a shared vision throughout, and the structure is clearly marked out from the beginning. Building relationships between staff will result in better collaboration, which is complemented by creating common technology platforms and specific, collaborative practices and contracts.
Which procurement method do we recommend?
All the routes discussed can be enabled through our frameworks, so we don’t have a favourite and make recommendations based on multiple criteria.
It’s important to remember these four types of procurement in construction and that they all share the goal of ensuring maximum project efficiency.
If you find yourself wanting to learn more about procurement with Pagabo then exploring our list of public sector frameworks is the perfect place to start.
Read our blog on Public Vs Private sector procurement:
View our public and private sector frameworks:
Discover our frameworks